MORE DATA, LESS MAINTENANCE
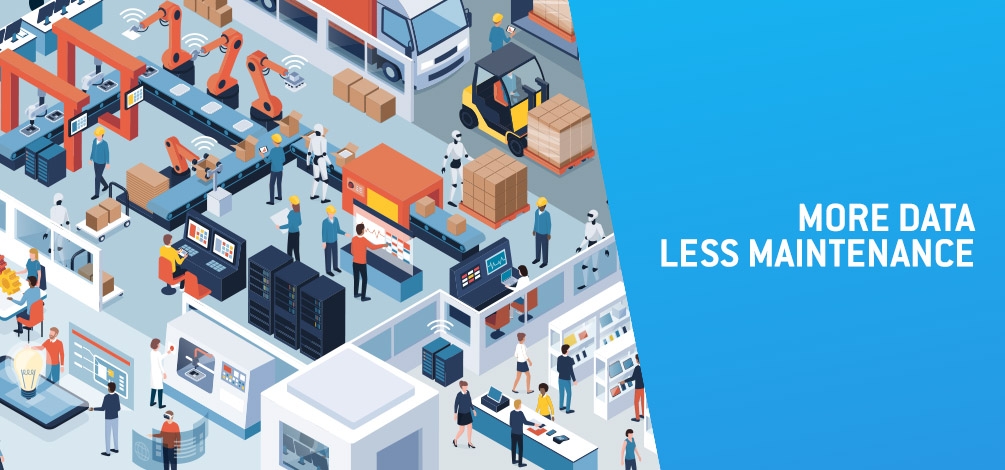
Industrial maintenance has undergone a revolution with the emergence of Industry 4.0. The status of production process and the equipment requires the monitoring of influencing variables in this process.
Every day, industrial environments are affected by failures and stops in the production process. It is a reality present in the equipment that perform repetitive tasks for a scaled production. A delay in production due to a forced break for maintenance can jeopardize the productive goals, lead to the increase of operational costs and non-fulfilment of deadlines. The industries aim to reach more profitable levels of efficiency and tend to adopt by the implementation of maintenance systems that help to reduce the rates of interventions of much needed industrial maintenance. The service significance is to ensure the upkeep the correct functioning of a production unit providing the necessary assistance to the manufacturing equipment.
Industrial maintenance has undergone a revolution with the emergence of Industry 4.0 concept. The idealization of intelligent systems integrated in the industrial process allowed to take advantage of the operational data surrounding the industrial environment and impact the productive stages making its elements more informed and proactive. The maintenance comes with new methods and more complex aspects arising from this change as is the case of predictive maintenance.
Predictive maintenance bases its intervention on the indications resulting from the monitoring of the equipment in order to trigger preventive actions to ensure the correct operation of the industrial plant. The consequent actions appear as preventive measures and not as corrective measures resulting from unexpected events that have already led to production chain breaks and increased operating and maintenance costs.
Predictive maintenance offers advantages that span the entire industrial system:
- Decrease machine downtime;
- Reduction in the number of unexpected interventions;
- Equipment life-time increased;
- Reduced maintenance costs;
- Productivity improvement;
- Increased workplace security;
- Reduction of industrial plant operating costs;
Internet of Things (IoT) come up as a technology to help this present of maintenance. Iths technological concept is linked to Industry 4.0 in the use of production data for a reliable monitoring of the productive system. The status of production process and the equipment requires the monitoring of influencing variables in this process – conductivity, pH, vibration, flow, humidity, level, pressure, temperature among others.
PLUS – from analog to IoT
Tekon Electronics has developed the PLUS wireless solution suit that streamlines the entire process of monitoring typical voltage and current analog variables.
The main feature of the PLUS wireless family is the collection of data from sensors. All this information generated by the sensors will soon be available online, in real time, for consultation and remote analysis through the Tekon IoT Platform.
How is data transmission processed? The TWP4AI transmitter supports the connection of up to 4 configurable analog inputs, turning traditional sensors in wireless smartsensors. One of the major breakthroughs in the reliability of communication available in the wireless PLUS system is the versatility of the TWP4AI transmitter also be able to play the repeater role.
Figure 1 - Tekon Configurator window with the TWP4AI transmitter double configuration
The encrypted data transmission range of this solution although extensive is limited, so the WRP001 repeater allows to extend the radius of action with the interconnection of up to 12 network repeaters in order to enhance the trust in data communication. Providing the correct data transmission also depends on the signal reliability. The transmitter and repeater of the PLUS product family carry out constant monitoring of the connection signal, data that is also stored and can be monitored on the Tekon IoT Platform.
The WGW420 gateway assumes the central role of this entire network solution, collecting information from up to 55 devices simultaneously, extending all of this data to the query and analysis on the Tekon IoT Platform.
The operational methodology of the PLUS wireless system focuses on a mesh type network typology. Benefits? This network typology redoubles the confidence in the connection to the users by the following indicators:
• Self-forming: seamless installation for the user. The network protocol performs all the necessary network input negotiation operations and chooses the information path between the TWP4AI transmitter and the WGW420 gateway;
• Auto healing: in case of data link breakage between devices, the network is able to search for and establish new connections between devices in order to maintain the correct operation of the network, all transparently and automatically without the need for user intervention;
• Multipath: the routing of a link becomes adaptable among several alternative paths within the network, causing greater security and reliability of the data package.
Figure 2 - Mesh network typology
PLUS wireless system features:
- Low power consumption;
- Supply voltage monitoring;
- Communication of devices located up to 4km (LoS) from each other;
- Supports up to 12 repeaters in series;
- Supports up to 55 transmitters in the same network;
- Mesh network typology;
FINAL CONCLUSIONS
In Industry 4.0, also known as the Fourth Industrial Revolution, with the emergence of new technologies, new maintenance processes emerged and drove the reformulation of past methods. The advances allowed the compilation of data to be translated into a more assertive response to the different difficulties in machines and production lines. The maintenance procedures culminated with an increase in the availability of equipment in industrial plants and in a greater control of cost of these processes.