Impact of Temperature and Humidity on Predictive Maintenance
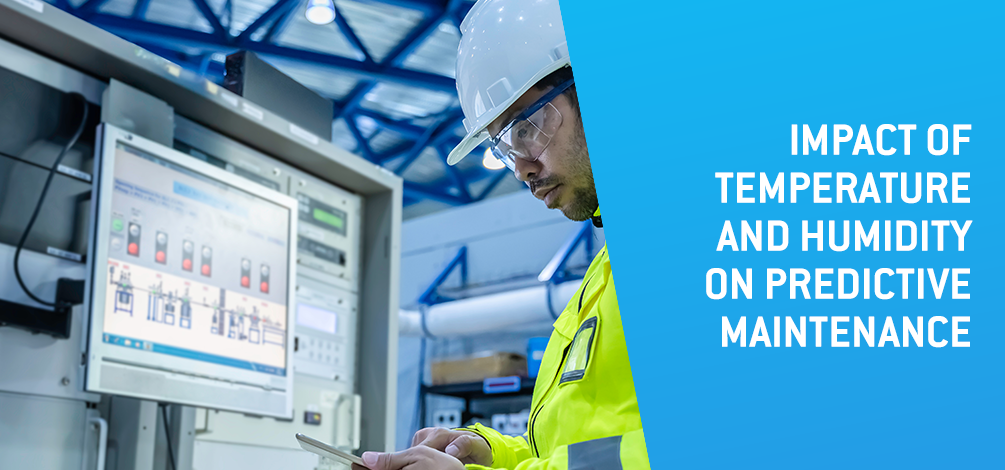
Monitoring environmental variables like temperature and humidity has a direct impact on predictive maintenance across various industries.
Predictive maintenance has revolutionized the way industrial equipment and facilities are managed, especially since the rise of Industry 4.0.
This approach relies on continuous monitoring of critical parameters to anticipate failures and schedule preventive actions at the right time.
Environmental variables are key parameters that directly influence the performance of machines and processes.
Current sensing solutions can continuously measure temperature, humidity, and many other variables, detecting problems at an early stage and preventing unexpected system failures.
Acting proactively with temperature data
When it comes to maintenance in industrial environments, temperature and humidity are critical and mandatory topics. They affect both the integrity of equipment and the quality of final products.
Thermal variations often signal emerging issues: lack of lubrication, imminent component failure, or electrical problems, to name a few.
Temperature sensors integrated into machines or in the factory environment continuously monitor these fluctuations.
This enables the early detection of deviations and overheating before they cause operational and financial disruptions.
Humidity and industrial environment maintenance
Relative humidity can also have a significant impact on certain applications.
Excessive humidity promotes corrosion of metal and electronic components, degrades electrical insulation, and can even lead to short circuits in critical factory equipment.
In sectors like the food industry, disproportionate humidity levels can spoil products, alter their properties, and lead to increased waste.
Maintenance teams benefit from tools that help them act preventively, such as Tekon Electronics’ DUOS Hygrotemp sensor.
By continuously monitoring temperature and relative humidity, it’s easier to act, replacing parts and equipment, triggering ventilation and HVAC systems, and addressing issues like leaks.
This kind of quick action today helps prevent higher expenses tomorrow, on multiple fronts.
Benefits of monitoring in predictive maintenance
Integrating sensors like Tekon’s DUOS into a proper predictive maintenance strategy delivers countless measurable benefits for industrial companies.
By tracking temperature, relative humidity, and other variables in real time, companies make maintenance more effective.
Key advantages include:
Fewer unexpected failures and downtimes
By detecting abnormal conditions early (e.g., overheating, excessive humidity), predictive maintenance drastically reduces unplanned machine downtime.
This proactive approach means fewer disruptions and shorter stoppages, avoiding losses that jeopardize deadlines and productivity goals.
With more reliable equipment, production lines run more consistently.
Maintaining optimal environmental conditions can even improve process quality. For example, getting more efficient drying times in painting processes thanks to humidity control.
Reduced maintenance and repair costs
Intervening before serious breakdowns means lower and fewer expenses.
Continuous monitoring allows for interventions when they’re truly needed, avoiding unnecessary maintenance and, above all things, major repairs from urgent issues.
As a result, companies save on resources like spare parts, labor hours, and unaligned services, ultimately easing the maintenance budget.
Extended equipment lifespan
Keeping environmental variables within ideal ranges leads to less wear and degradation.
A simple example: avoiding high-humidity environments helps reduce premature wear on motors and nearby components.
This means industrial assets last longer, maintain performance, and delay the need for replacements.
It’s a direct way to positively impact return on investment (ROI).
Quality assurance and regulatory compliance
In highly regulated industries (like food, pharmaceuticals, and electronics), keeping environmental variables within spec is crucial for product quality.
Predictive maintenance helps prevent anomalies that could compromise production batches or breach regulatory standards.
For example, avoiding temperature and humidity levels beyond the allowed range in a pharmaceutical production area ensures the quality and purity of the medicines.
On top of that, monitoring systems like the DUOS Hygrotemp paired with the Universal IoT Gateway are able to record continuous data, making it ready for analysis.
This data later serves as evidence during quality and safety audits, supporting compliance with regulations and laws.
Predictive maintenance is the smarter solution
Variable monitoring is clearly a powerful ally of predictive maintenance, and therefore of businesses across industry.
Wireless monitoring solutions like those from Tekon Electronics make it possible to install sensors at different stages of various processes.
That way, businesses across a wide range of industries reduce unpleasant surprises, lower costs, and boost efficiency.
Make your maintenance smarter, and your business more competitive.
Get in touch with us!