Smart Manufacturing - Industrial digital transformation
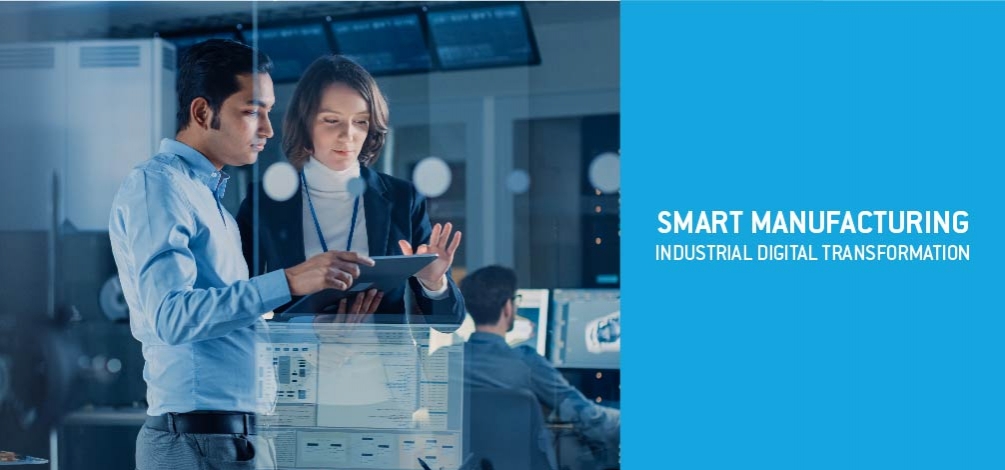
In recent years, the term Smart Manufacturing has been debated by industry experts, opinion leaders and consultants. Despite the constant dissemination and approach of the theme, this issue still raises many doubts for some organizations that want to position themselves at the forefront of production. Many of these doubts are related to the implications and relevance that this transformation can bring.
Capturing a part of the digital transformation opportunity is at the heart of business strategies today. In all industries, this represents an opportunity for an annual economic value of 17000 M € worldwide. The analysis, based on IDC research (December 2019), is focused on the impact of digital technology and looks across the value chain. Transformation is leading manufacturers to rethink their technological strategy and that includes the incorporation of innovation accelerators, such as the Internet of Things (IoT). Technological transformation addresses the alignment of strategic priorities for the industry:
- Supply chain optimization;
- Smart manufacturing;
- Innovative products;
- Customer experience;
In recent years, the term Smart Manufacturing has been debated by industry experts, opinion leaders and consultants. Despite the constant dissemination and approach of the theme, this issue still raises many doubts for some organizations that want to position themselves at the forefront of production. Many of these doubts are related to the implications and relevance that this transformation can bring. The Smart Manufacturing concept is very broad. Their understanding has given different perspectives between several entities. The Smart Manufacturing Leadership Coalition states that " Smart Manufacturing is the ability to solve existing and future problems via an open infrastructure that allows solutions to be implemented at the speed of business while creating advantaged value".
The goal of this concept is clear: to transform industrial production as it is known today into a networked architecture infrastructure, in which data is collected in real time, analyzed and used to improve the decision making related to the organization.
The most evident results provided by Smart Manufacturing are of high interest to the main agents:
- downtime decreasing;
- more efficient production;
- reduction in production costs;
- safer work environments;
- improvement in quality levels;
- more efficient maintenance;
The practical implementation on the production lines must be a progressive, step-by-step process. The existing equipment can be adapted in order to increase the use of the investment. The retrofitting of the already existing production mechanisms is a usual practice assumed by entrepreneurs where the value of Smart Manufacturing is not yet seen as a central investment. This behaviour has intensified the search for technological solutions that bring existing equipment closer to this renewing concept, capable of promoting a wider view of the entire organization.
The remodeling of infrastructures involves the creation of partnerships with partners that promote the installation of sensors that collect the data considered essential for each stage of the production process. With the new industrial revolution, known as Industry 4.0, the use of wireless sensors and transmitters has streamlined the remodeling procedures, offering connectivity that makes, in some cases, the use of wired systems that occupy and interfere in the industrial environment obsolete. The range of wireless networks between monitoring equipment, offers an extensive coverage area, with a small degree of interference in ongoing operations.
Real-time communication is now a reality that allows stakeholders to have faster access to the biggest asset in industries, regardless of the industry - real-time data. Each data collected assumes a key role in the set of data generated, thus allowing users to have access to an operational profile of the equipment. The transparency that the data shows is the point between the equipment and the decision makers. The degree of complexity and amount of data acquired in the industrial plant, is decomposed with data analysis. In this step, the interpretation of the information is performed based on the parameters specific to each application, where the context sets the focus of the analysis.
The decision base promoted by data analysis, supports decision making, which drives business and keeps the attention in the constant search for quality of products and services and productive performance. Assuming a non-financial perspective, the objective of quality assurance is one of the reasons that stimulates change and keeps the eye directed towards evolution.
A step to Smart Manufacturing
Tekon Electronics develops wireless solutions that promote the collection of data from the industrial plant. The remodeling of the production environment aims to absorb all data from variables of increased relevance to the production process. The centralization of data analysis in these variables, will allow the concept of Smart Manufacturing to have an implicit meaning in your organization.
The PLUS wireless system offers connectivity with analog and digital signal output sensors and transmits your registers through a dedicated wireless network, safeguarding the security and reliability of data transmission. The registers are organized on the Modbus map and can be acquired by local automation.
The PLUS wireless product family is a qualified solution by the following features:
- Acquisition of analog signals (4..20mA, 0..10V);
- Configurable digital inputs;
- Dedicated digital outputs;
- Networks with support for 55 transmitters;
- Communication range up to 4km (LoS);
- Monitoring connection status;
- Integration with automation (Modbus via RS-485);
- Data encryption;
Data visualization and analysis is the main function of the Tekon IoT Platform. A software solution, which can be used in the cloud or locally, where the graphical representation of the data in real time, offers to user the necessary tools to process the information depending on their application. The IoT platform allows to assimilate data and prepare the necessary decisions for the implementation of preventive or corrective measures on the shop floor.
The potential to interpret the data has a direct influence on achieving a cross-industry objective - OEE (Overall Equipment Effectiveness). A positive materialization of this objective is only possible if we use the data from our equipment, to promote the availability, performance, and quality rates. The analysis of production processes treats these three rates as essential to determine the condition of production and the loss of efficiency between the various parts.
Fonte: OEE Fundation
The key point is to use the data to fill gaps and add improvements to the productive environment.
Revolution with data
We are witnessing a revolution in the production processes of industrial units, originated by the value that wireless monitoring solutions have been adding in each context. The wave caused by Smart Manufacturing tends to implement digitalization, where the analog was ideal. The change may translate into adjustments in the front lines of companies, but it will keep the focus on proactivity and improving the quality of production processes.